Good Manufacturing Practices (GMP), commonly called current Good Manufacturing Practices (cGMP), are essential guidelines designed to ensure the consistent quality, safety, and integrity of products intended for human consumption, including dietary supplements, pharmaceuticals, and medical devices.
The Food and Drug Administration (FDA) and other regulatory agencies require that GMP covers key aspects of the manufacturing process, such as starting materials, quality control, and final product evaluation, ensuring that every finished product meets strict quality standards.
This guide explores what GMP entails, the key GMP requirements, and practical steps manufacturers can take to ensure compliance with federal regulations while mitigating the risks involved in production.
Table of Contents
ToggleWhat Are Good Manufacturing Practices (GMP)?
The Food and Drug Administration (FDA) defines Good Manufacturing Practices (GMP) as a set of regulations that manufacturers must follow to ensure that products are consistently produced and controlled according to strict quality standards. These GMP guidelines apply to every aspect of the manufacturing process to safeguard public health and ensure products are safe and effective for human consumption.
Why GMP Compliance Is Important
GMP compliance plays a vital role in protecting consumers and ensuring product integrity. Manufacturers maintain documented processes to demonstrate adherence to GMP guidelines and support quality assurance. Here’s why GMP compliance is essential:
- Ensures Safety: Reduces the risk of contamination or unsafe products.
- Maintains Quality: Ensures consistent quality across every manufactured product.
- Builds Consumer Trust: Demonstrates commitment to high-quality production.
- Meets Regulatory Requirements: Helps organizations comply with FDA and other regulatory agencies.
- Reduces Risks: Minimizes risks involved in the manufacturing process, such as contamination or mislabeling.
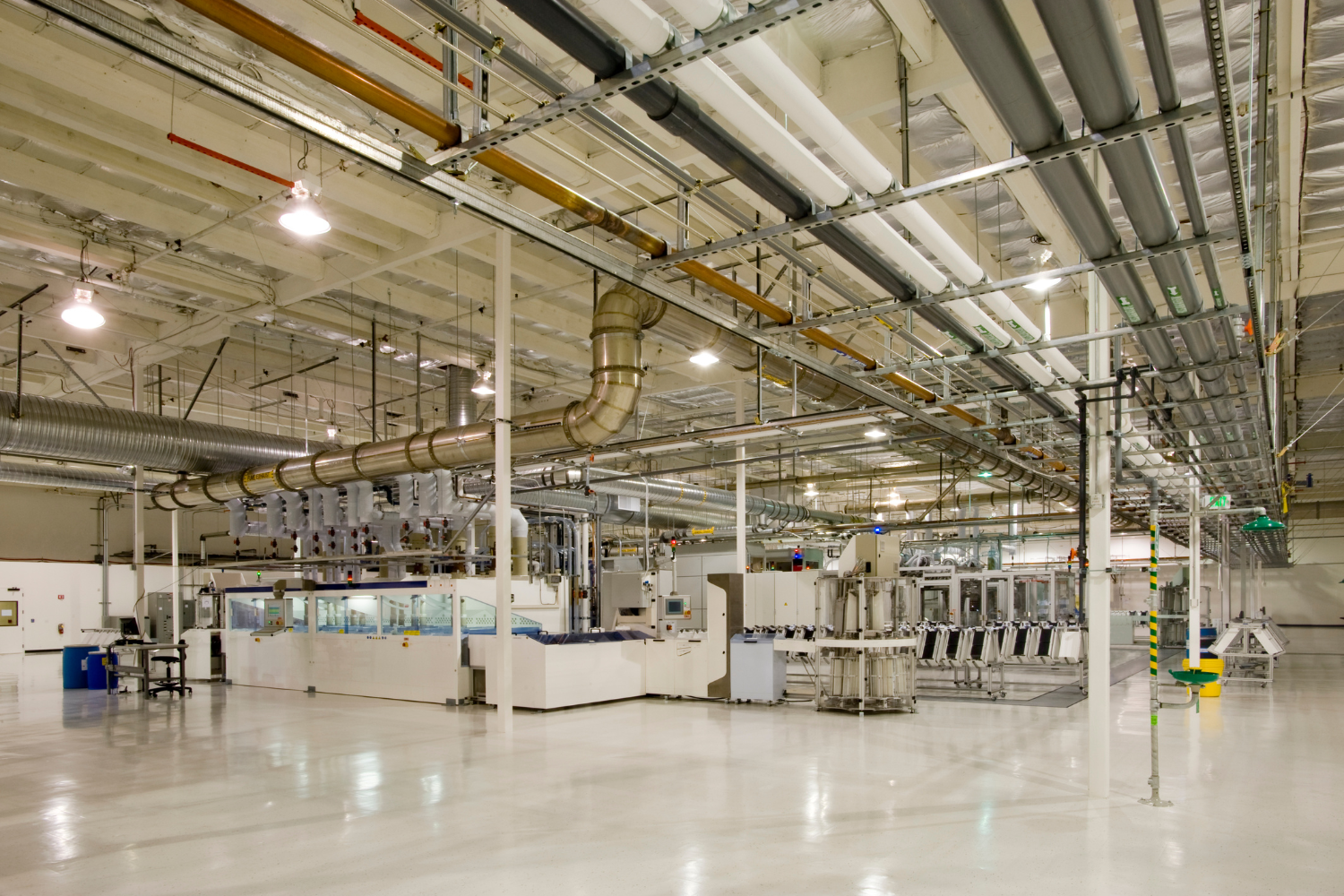
Key Components of Good Manufacturing Practices
Good Manufacturing Practices cover several critical areas to ensure products are consistently produced and controlled. Below are the main components of GMP compliance.
Clean and Sanitary Facilities
Maintaining clean and sanitary manufacturing facilities is a fundamental part of GMP compliance. A well-maintained environment prevents contamination and ensures products are consistently produced under safe conditions. Key aspects include:
- Sanitation Protocols: Regular cleaning and disinfecting of equipment and workspaces.
- Controlled Environment: Proper ventilation and temperature control to prevent contamination.
- Personnel Hygiene: Enforcing personal hygiene standards for all staff.
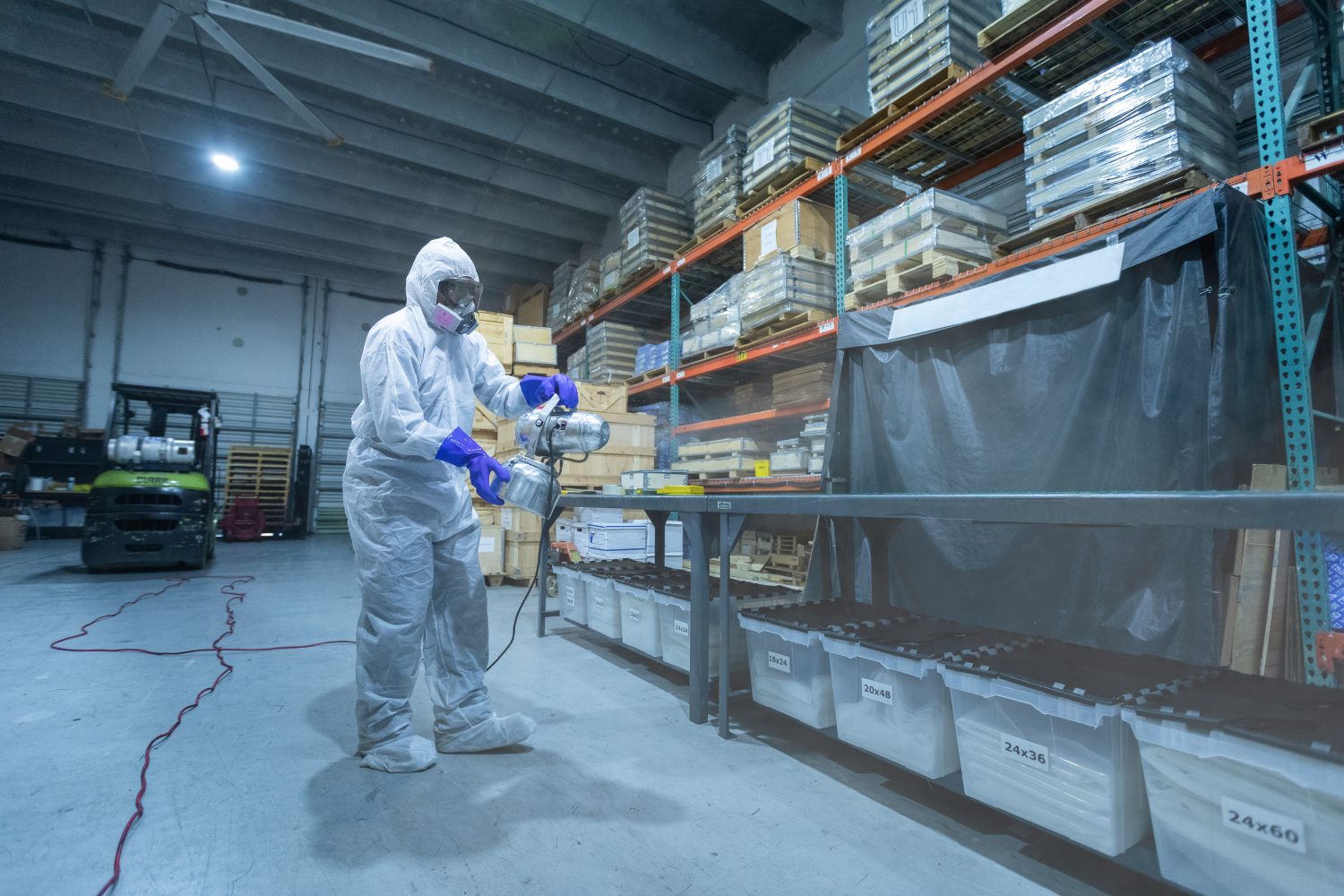
Proper Equipment Maintenance and Calibration
Regular maintenance and calibration of manufacturing equipment are critical for ensuring that products are consistently produced and controlled. Properly maintained equipment reduces the risk of mechanical failure, ensures accurate processes, and helps keep the integrity of the final product.
Raw Material Quality Control
Verifying the quality of raw materials is a crucial step in meeting GMP requirements. Manufacturers must source starting materials from reliable suppliers and conduct rigorous testing to ensure that all ingredients meet the required quality, safety, and purity standards before entering the manufacturing process.
Personnel Training and Hygiene
Proper training and hygiene are essential for everyone involved in the production process. Employees must be trained on GMP guidelines, including the correct procedures for handling materials, operating equipment, and maintaining cleanliness. Personal hygiene practices also play a critical role in preventing contamination and ensuring consistent product quality.
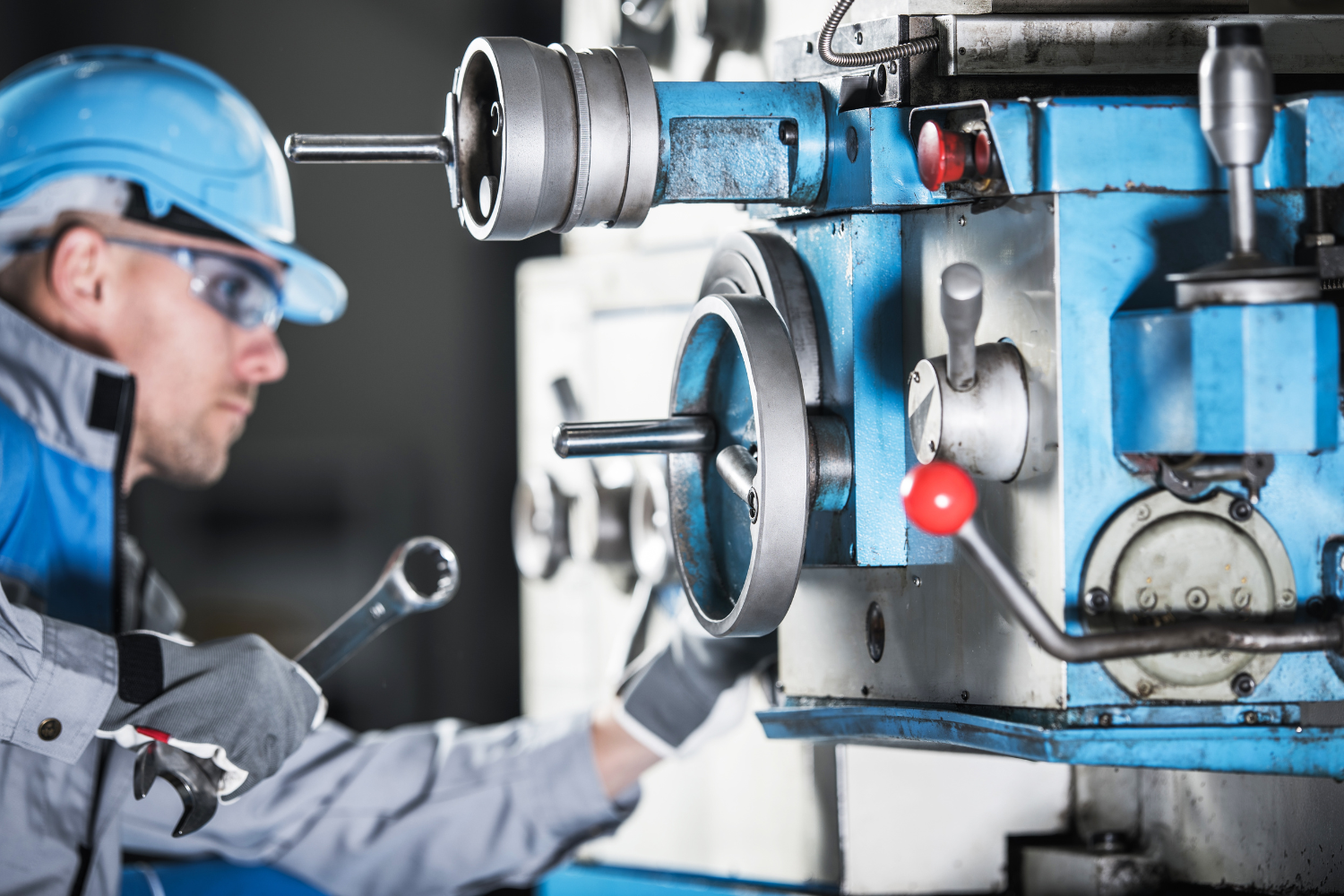
Documentation and Record-Keeping
Comprehensive documentation is a cornerstone of GMP compliance. Manufacturers must document procedures, ingredient sourcing, process validation, and quality control measures. Detailed records provide evidence that products have been consistently produced and controlled, which is essential for FDA inspections and compliance with federal regulations.
Steps to Ensure Your Product Complies with GMP
Ensuring your product complies with Good Manufacturing Practices involves proactive steps to meet FDA standards. These measures help maintain consistent quality and safety throughout the manufacturing process, from facility audits to quality control systems.
Conduct a GMP Audit of Your Facility
Regular GMP audits are essential to ensure compliance with federal regulations and identify potential areas for improvement. These audits can be conducted internally or by third-party auditors specializing in GMP compliance. Key benefits of conducting GMP audits include:
- Identifying Weaknesses: Spot areas in your manufacturing process that may not meet GMP standards.
- Enhancing Processes: Improve procedures to ensure consistently produced and controlled products.
- Providing Documented Proof: Demonstrate GMP compliance to regulatory agencies like the FDA.
- Minimizing Risks: Address risks involved in production, such as contamination or mislabeling.
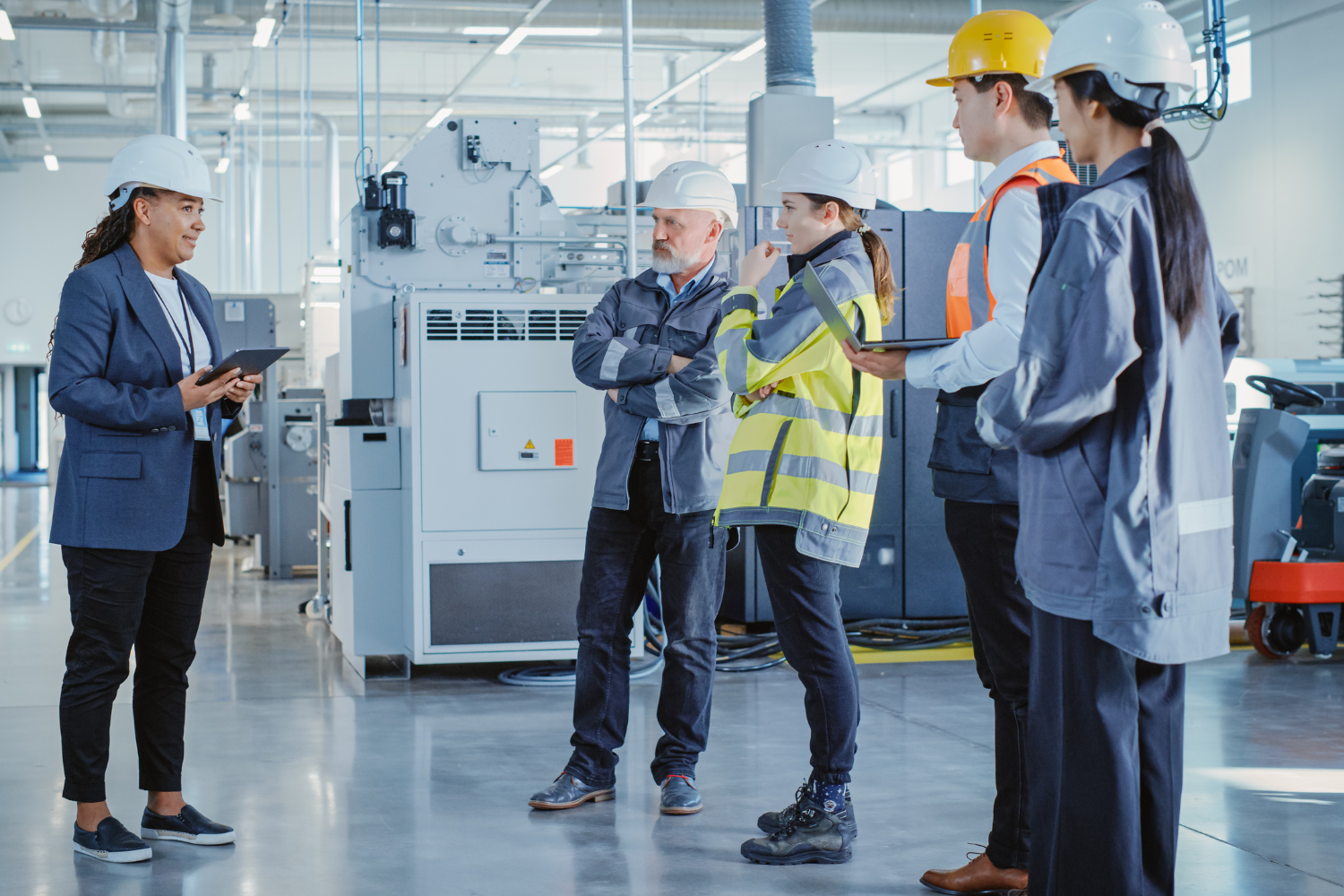
Implement a Quality Control System
A robust quality control system is a cornerstone of GMP compliance. Implementing standard operating procedures (SOPs) ensures consistent production and adherence to quality standards.
- Consistency: SOPs ensure every manufacturing process follows the same approved methods.
- Accuracy: Prevent errors by clearly defining processes for handling starting materials and equipment.
- Sanitation: Establish protocols for maintaining clean and safe manufacturing facilities.
Testing products during and after production helps verify that the finished product aligns with label claims, GMP regulations, and quality specifications and upholds quality specifications, ultimately protecting the manufacturer and the consumer.
Establish a Corrective and Preventive Action (CAPA) Plan
A Corrective and Preventive Action (CAPA) plan helps manufacturers address issues that arise during production and prevent future deviations from GMP standards. By identifying root causes and implementing corrective measures, a CAPA plan ensures your manufacturing process remains compliant and reduces product quality and safety risks.
Labeling and Packaging Compliance with GMP
Labeling and packaging are crucial aspects of GMP compliance. They ensure that products are accurately represented and protected from contamination.
FDA Labeling Requirements
To comply with FDA regulations, manufacturers must ensure that product labels meet strict requirements for accuracy and transparency. These minimum requirements include:
- Supplement Facts Panel: Accurately list serving size, nutrient content, and percent daily values.
- Ingredient List: Include all ingredients used in the product in descending order of weight.
- Claims Compliance: Avoid unsubstantiated or misleading claims about the product’s benefits.
- Allergen Information: Clearly state if the product contains allergens or was manufactured in a facility that processes them.
Packaging Quality and Tamper-Evidence
High-quality, tamper-evident packaging protects product integrity and ensures safety during shipping and handling. Using secure packaging materials and tamper-proof seals gives consumers confidence in the product while reducing risks of contamination or damage to the finished product.
The Role of Third-Party Certification in GMP Compliance
Third-party certification is a valuable tool for manufacturers looking to demonstrate their commitment to Good Manufacturing Practices. Certification from organizations like NSF, UL, or USP provides an additional layer of quality assurance, signaling to consumers and retailers that products meet rigorous safety and quality standards. Key benefits of third-party certification include:
- Enhanced Credibility: Builds trust with customers and partners by validating GMP compliance.
- Market Access: Increases opportunities to work with retailers and distributors requiring certification.
- Risk Reduction: Identifies potential GMP issues before regulatory inspections.
- Consumer Confidence: Reassures consumers that products are consistently produced and controlled.
How to Obtain Third-Party Certification
Obtaining third-party GMP certification involves verifying that your manufacturing processes meet current Good Manufacturing Practices. These steps typically include:
- Initial Audit: A thorough review of your facility and manufacturing process by a third-party auditor.
- Documentation Review: Verification of SOPs, quality control measures, and record-keeping systems.
- Corrective Actions: Addressing any issues identified during the audit.
- Certification Approval: Receiving official certification once all requirements are met.
- Ongoing Compliance Checks: Regular audits to ensure continued adherence to GMP standards.
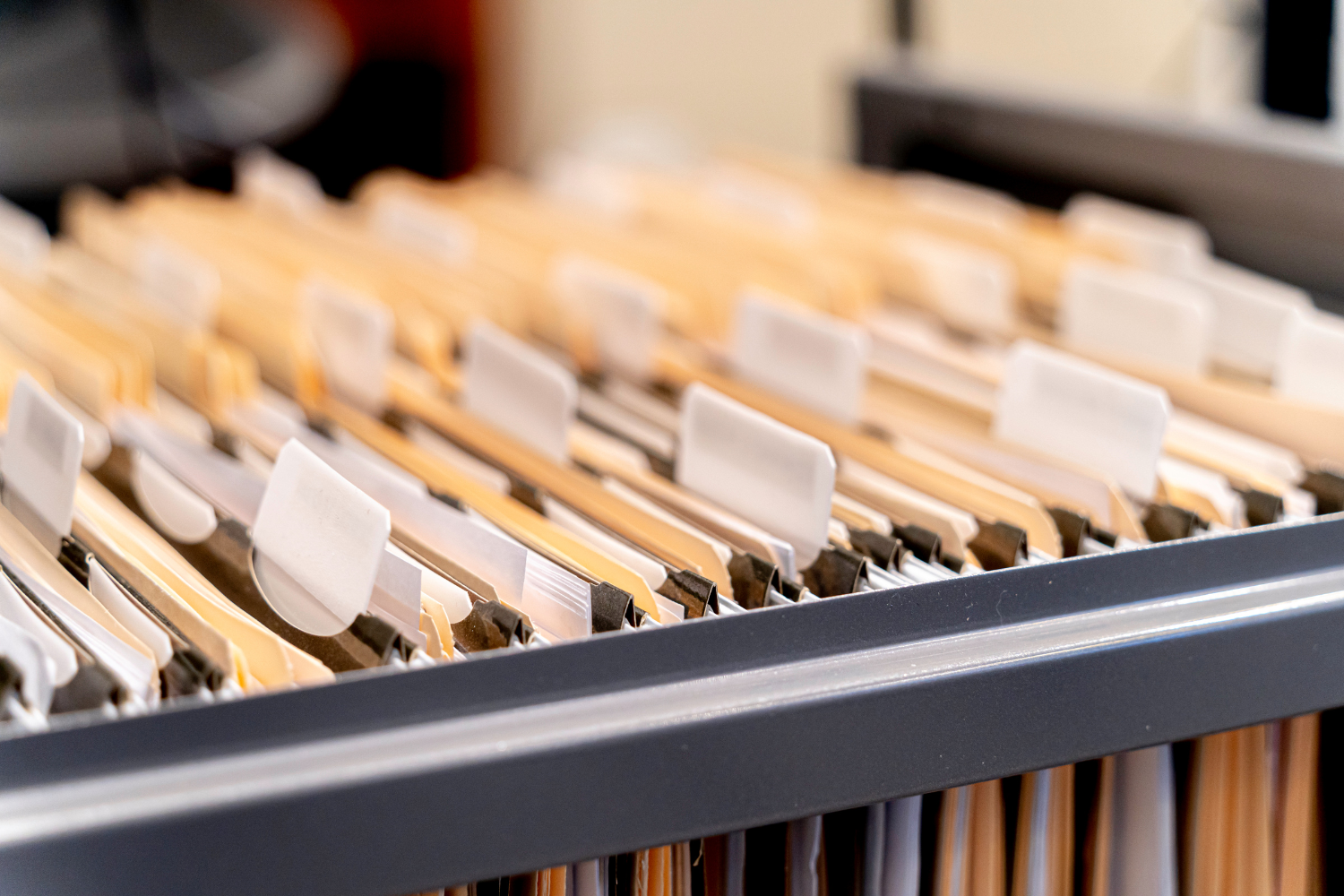
FDA Inspections and Ensuring Ongoing GMP Compliance
FDA inspections are critical to GMP enforcement, ensuring facilities comply with federal regulations. Manufacturers must proactively maintain compliance to avoid penalties and ensure product quality.
Preparing for FDA Inspections
Preparing for an FDA inspection requires careful organization and readiness. Facilities should have all necessary records and systems in place to demonstrate compliance with GMP guidelines. Key preparation steps include:
- Organize Documentation: Ensure production records, SOPs, and quality control logs are up to date.
- Conduct Mock Audits: Simulate FDA inspections to identify and address potential gaps.
- Train Personnel: Educate staff on FDA inspection procedures and GMP requirements.
- Demonstrate Processes: Be prepared to showcase manufacturing processes and testing protocols.
Maintaining Continuous Compliance
Ongoing GMP compliance requires regular attention to quality management systems and regulatory updates. Manufacturers should conduct routine internal audits, stay informed on changes to FDA guidelines, and continually improve their processes to ensure consistent quality. This proactive approach minimizes risks, protects product integrity, and provides long-term compliance with GMP standards.
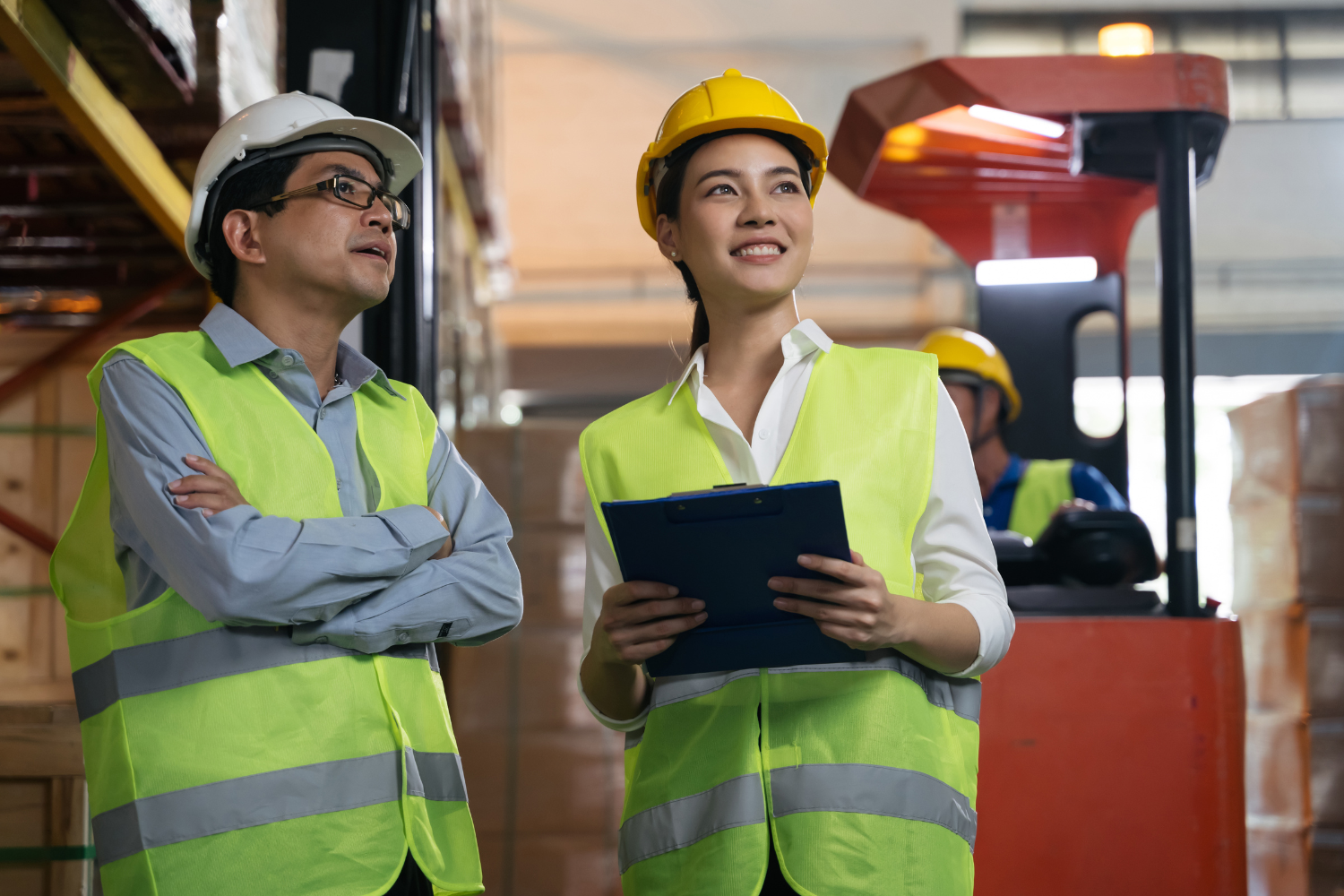
Ensuring GMP Compliance for Quality and Trust
Good Manufacturing Practices (GMP) are vital for producing safe, effective, high-quality dietary supplements and nutrition products. Adhering to GMP requirements, such as maintaining clean facilities, implementing robust quality control systems, and keeping thorough documentation, can help you meet FDA regulations while earning consumer trust. For expert guidance in ensuring your product complies with GMP standards, consider scheduling a consultation with our team to support your journey to compliance.
Frequently Asked Questions
What are the minimum requirements of GMP?
GMP requirements include maintaining clean facilities, documenting procedures, implementing quality control systems, and training personnel on compliance standards.
How do I know if my facility meets GMP standards?
You can determine compliance by conducting internal audits or hiring third-party auditors to evaluate your facility against GMP regulations.
Do I need third-party certification for GMP compliance?
While not mandatory, third-party certification enhances credibility, builds consumer trust, and helps ensure adherence to GMP standards.
What does GMP cover in manufacturing?
GMP covers all aspects of manufacturing, including sanitation, equipment maintenance, personnel training, raw material quality, and documentation.
Why is GMP important in the supplement industry?
GMP helps manufacturers produce dietary supplements that are consistent, meet quality standards, and minimize risks to consumers.
References
- U.S. Department of Agriculture. (2022). Good Manufacturing Practices Audits. https://www.ams.usda.gov/services/auditing/gmp
- U.S. Department of Agriculture. (2020). Guidebook for the Preparation of HACCP Plans. https://www.fsis.usda.gov/guidelines/2020-0008
- U.S. Food and Drug Administration. (2023). Current Good Manufacturing Practice (CGMP) Regulations. https://www.fda.gov/drugs/pharmaceutical-quality-resources/current-good-manufacturing-practice-cgmp-regulations
- U.S. Food and Drug Administration. (2024). Facts About the Current Good Manufacturing Practice (CGMP). https://www.fda.gov/drugs/pharmaceutical-quality-resources/facts-about-current-good-manufacturing-practice-cgmp
- U.S. Food and Drug Administration. (2023). Good Manufacturing Practice (GMP) Guidelines/Inspection Checklist for Cosmetics. https://www.fda.gov/cosmetics/cosmetics-guidance-documents/good-manufacturing-practice-gmp-guidelinesinspection-checklist-cosmetics
- U.S. Food and Drug Administration. (2023). Q&A on CGMP Requirements. https://www.fda.gov/drugs/pharmaceutical-quality-resources/qa-cgmp-requirements