Understanding supplement manufacturing lead times is critical for entrepreneurs, brand builders, and product managers looking to enter or grow within the dietary supplement industry. Lead times directly impact your ability to meet consumer demand, align with production schedules, and avoid missed opportunities in the competitive supplement market. This article breaks down how long it typically takes to manufacture nutritional supplements, what factors influence the timeline, and practical steps you can take to streamline the entire process.
From raw materials and custom formulations to quality control standards and regulatory compliance, you’ll understand what affects production and how to work with supplement manufacturers to deliver high-quality control standards on time.
Table of Contents
ToggleWhat Does ‘Lead Time’ Mean in Supplement Manufacturing?
Lead time in supplement manufacturing refers to the total time it takes from the start of your order to when the finished product is ready to ship. This includes everything from product formulation, ingredient sourcing, and production to quality assurance, custom packaging, and delivery.
The full timeline can stretch over several weeks, depending on your order type and the manufacturer’s production capacity. Delays in lead time can affect your ability to manage inventory, meet marketing deadlines, and execute your product launch. Understanding how long the entire process takes helps you make informed business decisions and keep your supplement brand on schedule.
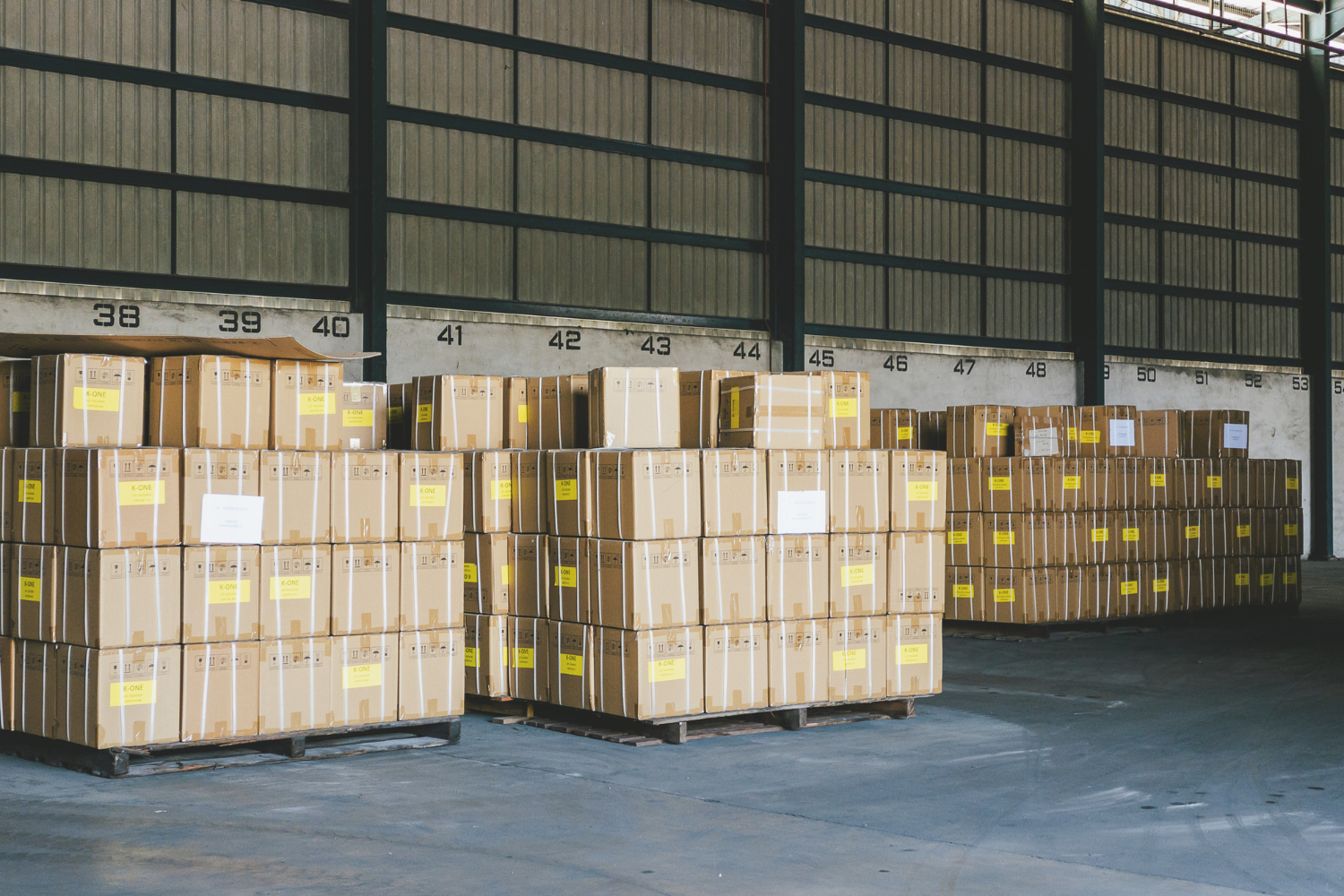
What Are the Typical Lead Times for Supplements?
Lead times vary based on the product type, the services offered by the supplement manufacturer, and the complexity of your order. Knowing the average timelines can help you plan and avoid production delays.
General Lead Time Ranges (Average Weeks)
Most supplement manufacturers follow general timeframes depending on the nature of the order:
- Custom formulation (8–16 weeks): Includes product development, sourcing high-quality raw materials, and required stability testing.
- Private label (4–8 weeks): Uses pre-formulated options, which reduces manufacturing lead times.
- Stock formulas (2–4 weeks): Fastest turnaround with minimal customization, ideal for fast market entry.
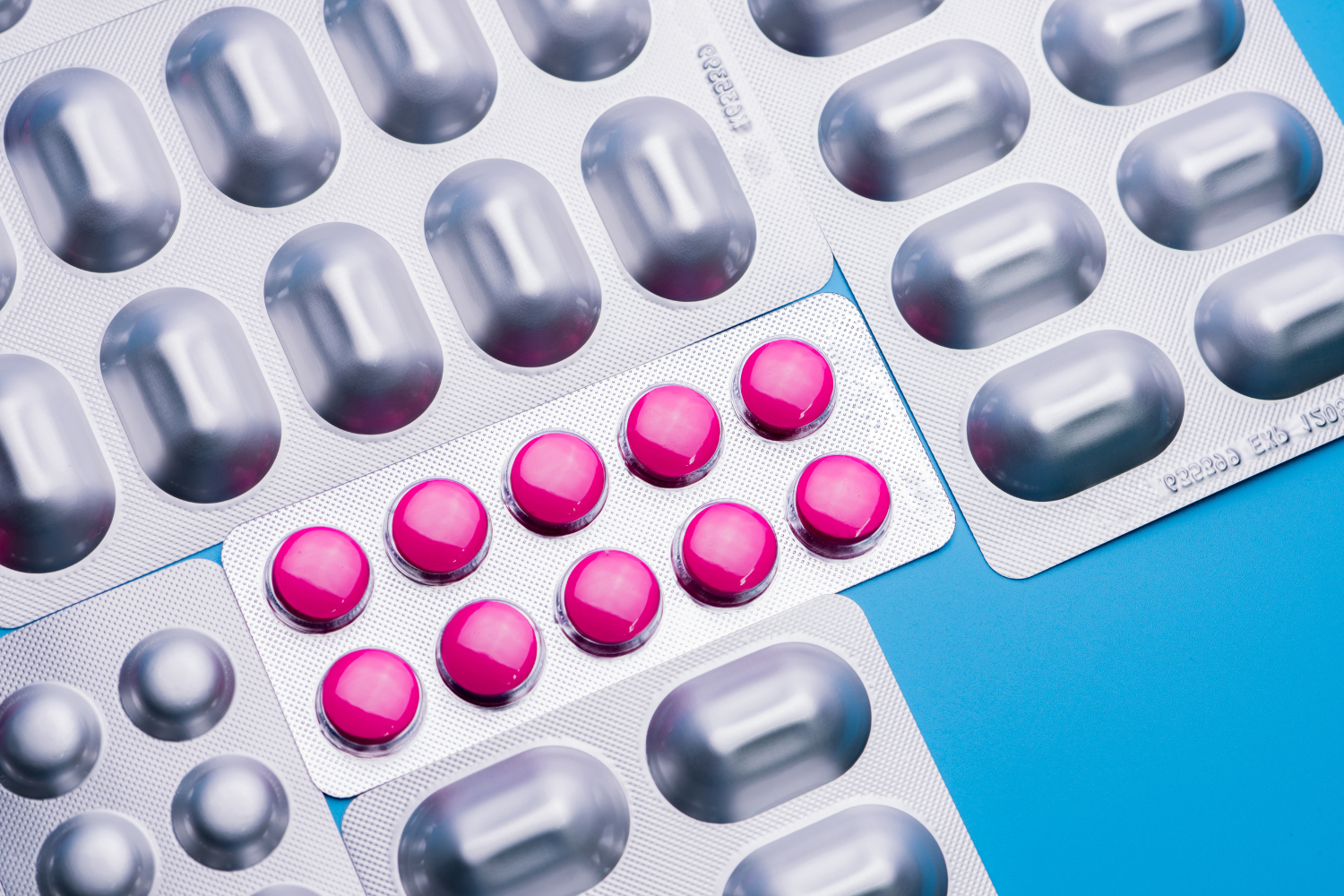
Lead Time by Product Type
Different product forms require different equipment and processes, which affects how long it takes to produce them.
- Capsules: Usually 4–8 weeks, depending on the number of key ingredients and quality control checks.
- Powders: 6–10 weeks, especially when using fine powders or requesting custom formulations.
- Gummies: 8–12 weeks due to complex manufacturing processes and additional testing for consistency.
- Liquids: 6–10 weeks, factoring in fill rates, preservation, and regulatory compliance.
- Stick packs & sachets: 8–14 weeks, depending on materials and custom packaging availability.
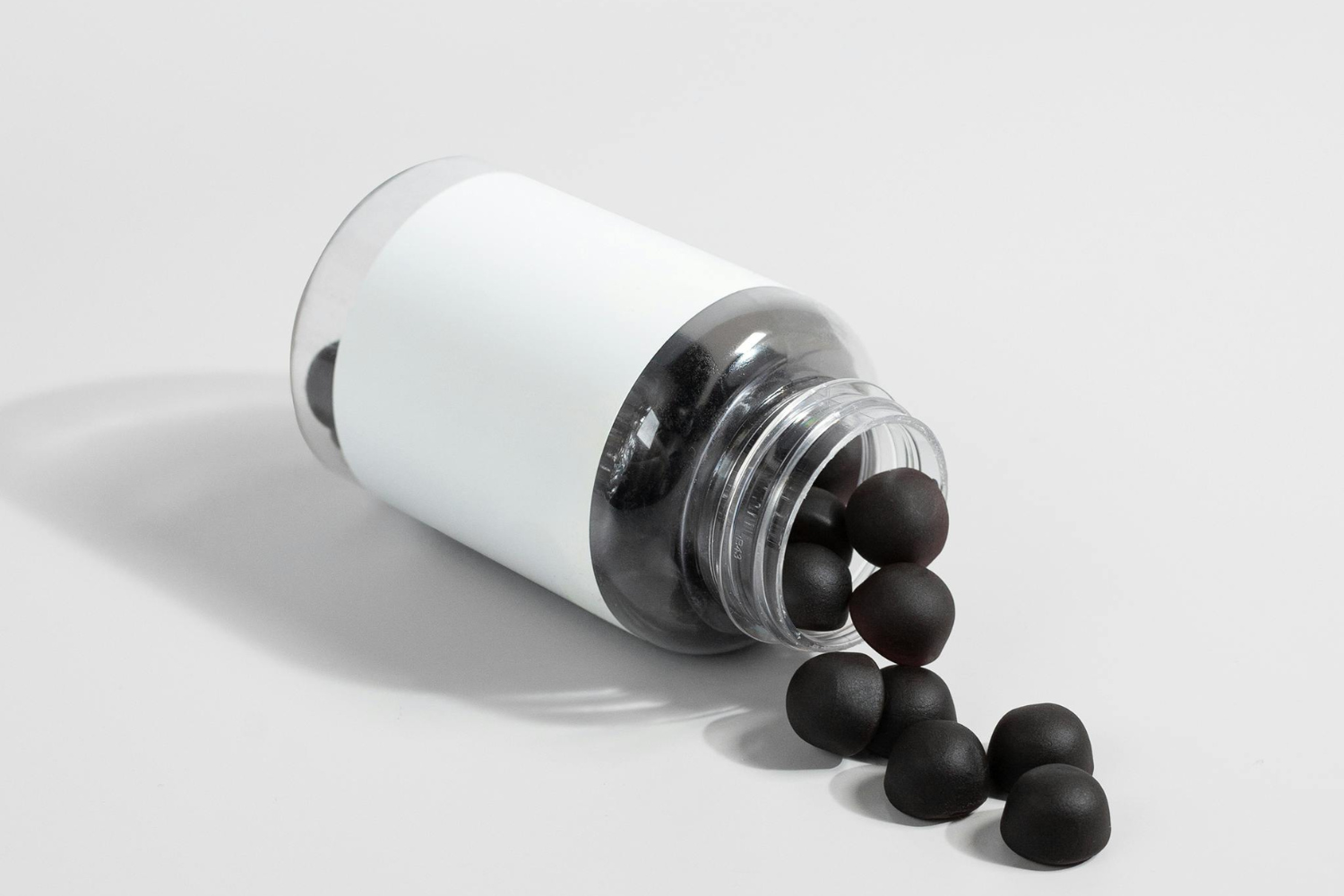
How Packaging Format Affects Lead Time
Your packaging format directly impacts how quickly your dietary supplement is ready for market. Bulk packaging—used for internal repackaging or wholesale—generally has shorter lead times than retail-ready formats that require labeling, sealing, and boxing.
The format you choose, such as bottles, pouches, or blister packs, adds different levels of complexity. For example, blister packs often require special tooling and sealing equipment, increasing time and cost. Choosing packaging aligned with your production goals helps reduce unnecessary delays.
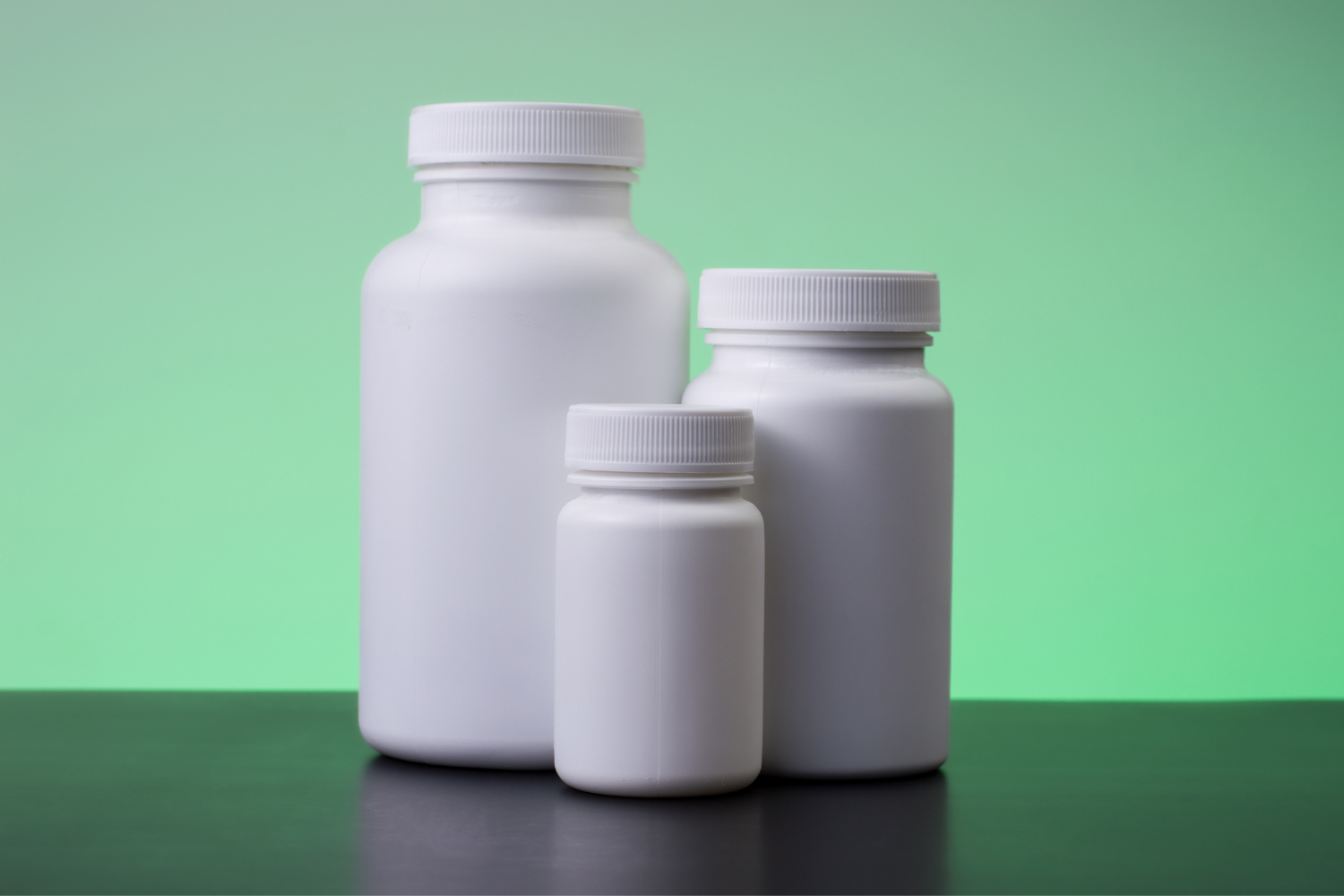
What Factors Can Affect Supplement Manufacturing Lead Times?
Several key factors can impact how long it takes to complete the supplement manufacturing process. These issues can slow down timelines and affect how soon your finished product reaches the market.
Ingredient Sourcing Delays
Sourcing raw materials—especially rare or certified organic ingredients—can lead to delays. Some high quality raw materials are only available from international suppliers, which increases the risk of shipping issues, customs holdups, or supply chain disruptions. Inconsistent access to ingredients can affect production schedules and quality control standards.
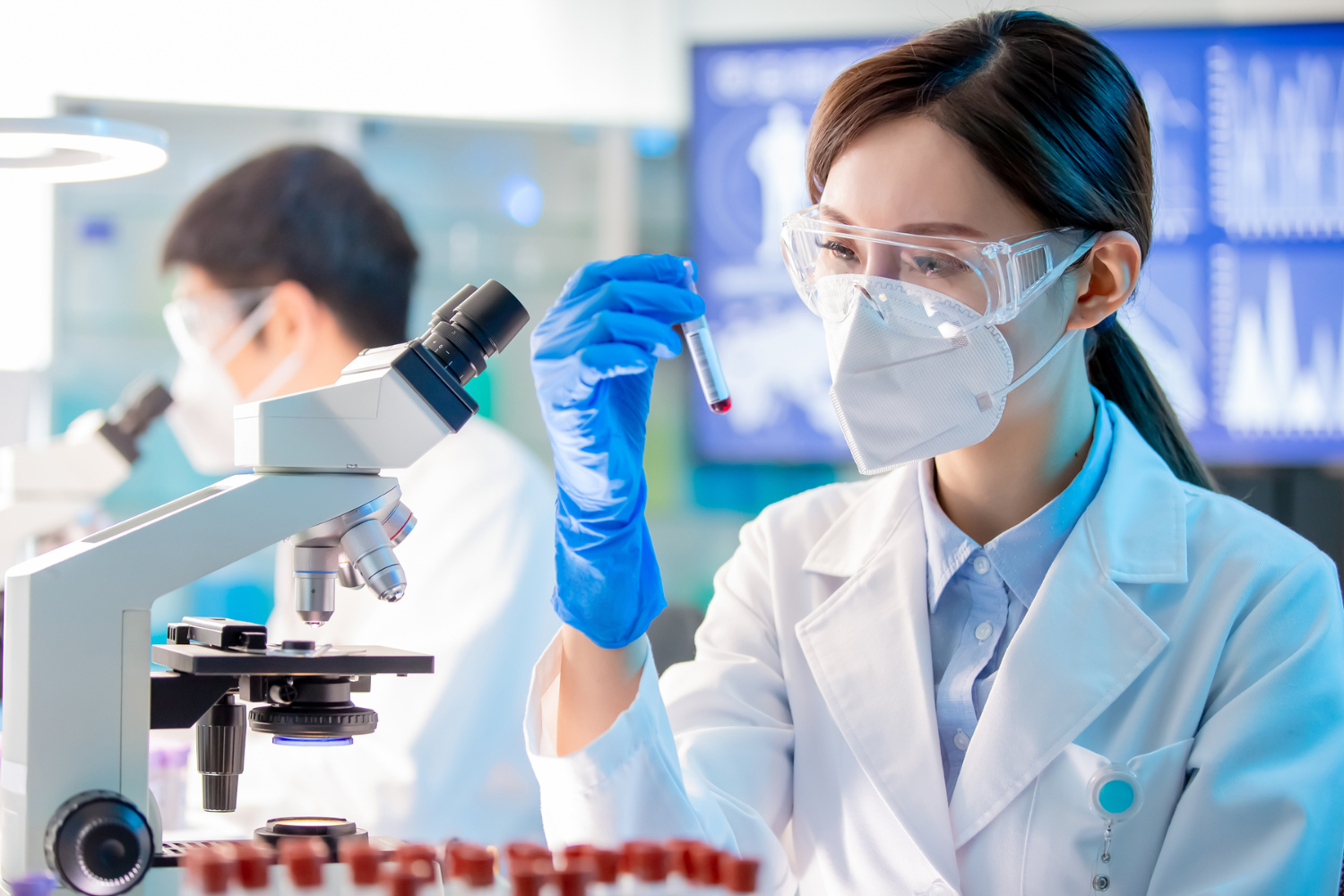
Formulation Complexity and Customization
A brand-new formula takes longer than using a stock formula because it requires R&D, stability testing, and approval steps. Creating a custom formulation means each ingredient should be evaluated for formulation compatibility, taste, and applicable regulatory considerations, which adds weeks to the manufacturing process. Choosing an existing base formula helps reduce the timeline.
Quality Control and Batch Testing
Most manufacturers include COAs, heavy metal testing, and third-party lab analysis as part of their quality assurance process to help meet regulatory standards and internal quality control protocols. If testing results don’t meet industry standards, products may require retesting, which adds to the delay.
Packaging Availability and Custom Design
Custom packaging, including bottles, labels, and inserts, takes time to design and print. If dielines are not finalized early or if materials are out of stock, delays are likely. Custom retail-ready options like blister packs or shrink sleeves often require extra design approvals and production time, slowing down the entire process.
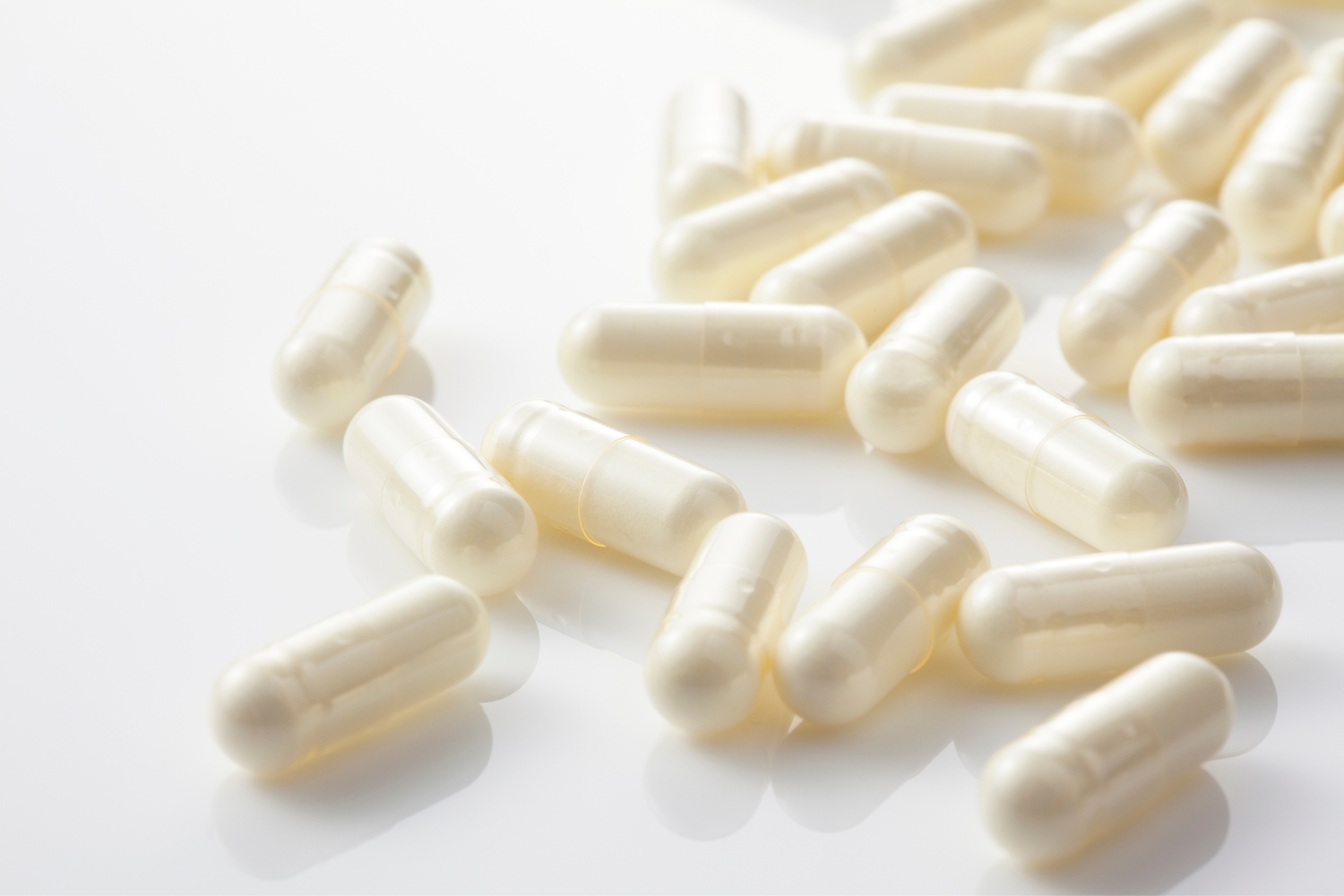
Manufacturing Queue and Facility Capacity
A manufacturer’s production capacity plays a significant role in determining lead times. During high-demand seasons, such as Q3 and Q4, manufacturing facilities often operate on a first-come, first-served basis. If your project enters the queue late or the manufacturer is already working on large minimum order quantities, you may need to wait longer.
Shipping and Fulfillment Logistics
Once products are ready, shipping times will still affect the final delivery. Domestic shipping is usually faster, while international delivery may face customs delays or longer transit. Carrier issues like weather or port congestion can add unexpected time to the end of the production cycle, even when manufacturing is complete.
How Can You Reduce Supplement Lead Times?
Planning ahead and working with experienced supplement manufacturers can help shorten manufacturing lead times and improve your time to market.
Use Stock Formulas or Private Label Options First
Starting with private label or stock formulas is the fastest way to enter the supplement market. These options require lower minimum order quantities and come with pre-tested formulas, helping you launch faster while you plan for future custom formulations.
Work With Manufacturers Who Keep Ingredients In Stock
Ask your private label manufacturer if they stock key ingredients or partner with trusted suppliers. Having ingredients on hand cuts down on sourcing time and helps prevent delays caused by supply chain issues or international shipping problems.
Finalize Packaging Early
Get your custom packaging designs approved early in the process. Waiting too long to approve dielines, labels, or inserts can delay the whole project. Early coordination allows packaging production to run alongside supplement production, saving time.
Keep Communication Clear and Fast
Most production delays can be traced back to miscommunication. Ensure your team communicates formula changes, packaging updates, and timeline expectations. Responding quickly to manufacturer questions helps avoid bottlenecks.
Ask About Lead Times in Your Contract
Include detailed manufacturing lead times in your contract, covering steps like production, additional testing, packaging, and delivery. An explicit agreement sets expectations and ensures the manufacturer’s commitment to a timeline that supports your business’s growth and keeps your supplement brand on track.

Common Mistakes Entrepreneurs Make With Lead Times
Planning a supplement launch without understanding the whole manufacturing process can lead to setbacks. New business owners and even experienced brand builders often encounter avoidable issues that delay their final product. Being aware of these common mistakes helps keep your supplement brand on track.
Waiting Too Long to Start the Process
Many entrepreneurs underestimate how long supplement manufacturing takes and start the process too close to their target launch date. Delays in ingredient sourcing, custom packaging, or testing can easily push production back, especially during busy seasons or when working with custom formulations.
Assuming All Product Types Take the Same Time
Each product type—capsules, gummies, powders, liquids, or stick packs—has a different production timeline. Assuming they’re all the same can cause errors in planning. Some require more stability testing or special equipment, which increases manufacturing lead times.
Not Asking for Timeline Estimates During Sales Calls
Skipping the question about lead times during initial discussions with supplement manufacturers can lead to surprises later. Without a precise estimate, planning your marketing, inventory, or fulfillment logistics is hard. Asking upfront helps avoid confusion and sets better expectations.
Skipping Packaging Planning Until the Last Minute
Leaving custom packaging decisions until late in the process slows everything down. Designing, printing, and approving labels or retail-ready components takes time. Packaging delays can slow final delivery, especially for retail-ready formats, even when the product is already produced.
Failing to Build in a Buffer for Unexpected Delays
No matter how well things are planned, delays can still happen due to quality control, regulatory compliance, or carrier-related issues. Without buffer time in your calendar, these setbacks can lead to missed launch dates and lost sales opportunities.
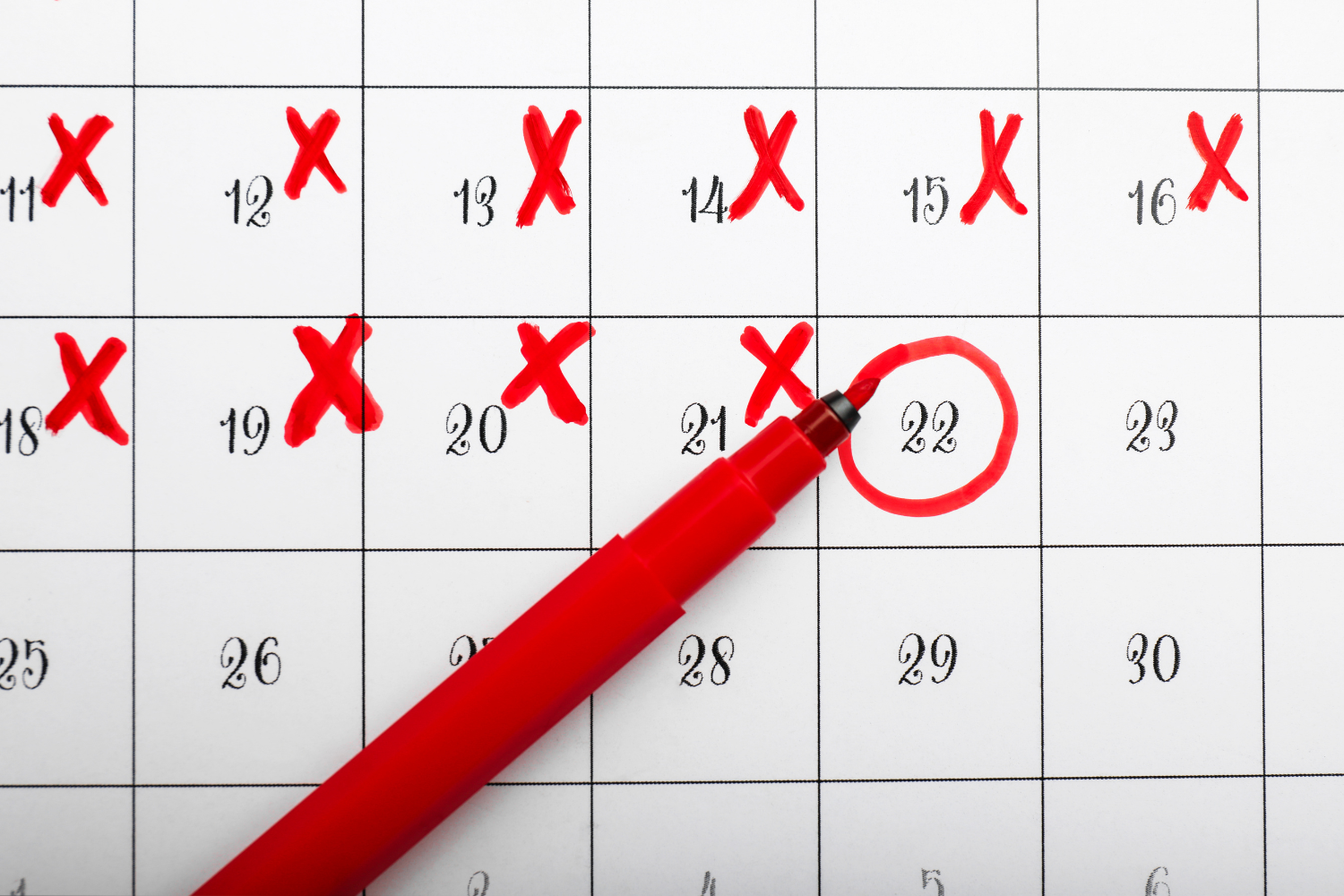
How to Set Better Expectations With Your Manufacturer
Clear communication and planning can help avoid confusion during supplement manufacturing. Setting expectations early with your private label manufacturer helps keep your project on schedule and supports your business’s growth.
Ask for a Step-by-Step Production Timeline
Request a detailed breakdown of the production process, including:
- Ingredient sourcing
- Custom formulation or stock formula prep
- Quality control and testing
- Packaging design and approval
- Final production and assembly
- Fulfillment and shipping
Schedule Buffer Time Into Your Launch Calendar
Build extra time to account for production delays, testing retakes, or packaging holdups. A 2–3 week buffer allows smoother operations and helps reduce the risk of delays or compliance issues that could lead to product recalls.
Stay in Regular Contact for Updates
Check in with your manufacturer at each stage of the process. Regular updates help you stay informed, spot potential delays early, and make adjustments if needed. Good communication also helps maintain trust with your supplier.
Get Clarity on What Happens If There’s a Delay
Ask what the process looks like if there’s a delay in any step—ingredient sourcing, batch testing, or shipping. Know if backup suppliers are used, how often updates are shared, and who to contact. Clear answers reflect the manufacturer’s commitment to quality and transparency.
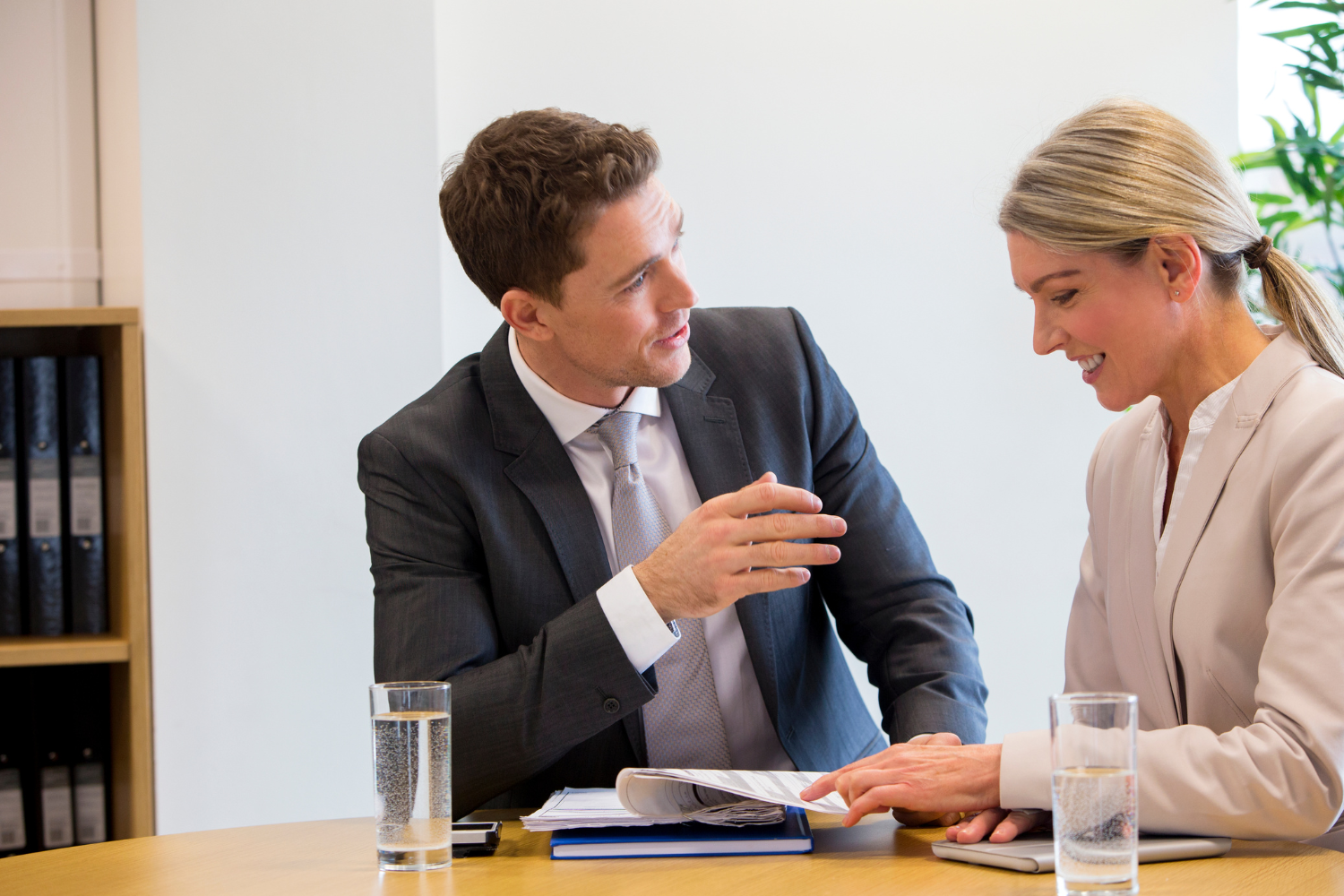
Plan Ahead and Stay Ahead With Lead Times
Supplement manufacturing lead times vary depending on your formula, packaging, and the manufacturer’s production capacity, but most delays can be avoided with early planning and clear communication. Understanding the full production timeline helps you align your supplement brand with consumer demand and prevent unexpected slowdowns in your supply chain.
Strong coordination with your private label manufacturer, early packaging decisions, and choosing reliable partners with available high quality raw materials make a big difference in staying on schedule. To help you stay organized, download our free Supplement Launch Timeline Checklist and simplify your planning process.
Frequently Asked Questions
How long does it take to manufacture a supplement?
Manufacturing timelines typically range from 2 to over 16 weeks, depending on the type of supplement, formulation complexity, and production requirements.
What can cause delays in supplement manufacturing?
Delays often come from ingredient sourcing issues, custom packaging lead times, or extended quality control and testing.
Can I reduce lead time if I use a stock formula?
Yes, using a stock formula can cut lead times to as little as 2–4 weeks since the formulation and testing are already complete.
How do I speed up the supplement production process?
You can speed up the process by choosing a private label option, finalizing packaging early, and working with manufacturers who stock ingredients.
Is packaging included in the manufacturing lead time?
Yes, custom packaging like bottles, labels, and inserts is part of the total manufacturing lead time and can add several weeks if not planned early.
References
- Code of Federal Regulations. (2025). Tamper-evident packaging requirements for over-the-counter (OTC) human drug products. https://www.ecfr.gov/current/title-21/chapter-I/subchapter-C/part-211/subpart-G/section-211.132
- U.S. Food & Drug Administration. (2020). Botanical Drug Development: Guidance for Industry. https://www.fda.gov/regulatory-information/search-fda-guidance-documents/botanical-drug-development-guidance-industry
- U.S. Food & Drug Administration. (2025). Closer to Zero: Reducing Childhood Exposure to Contaminants from Foods. https://www.fda.gov/food/environmental-contaminants-food/closer-zero-reducing-childhood-exposure-contaminants-foods
- U.S. Food & Drug Administration. (2024). Current Good Manufacturing Practices (CGMPs) for Food and Dietary Supplements. https://www.fda.gov/food/guidance-regulation-food-and-dietary-supplements/current-good-manufacturing-practices-cgmps-food-and-dietary-supplements
- U.S. Food & Drug Administration. (2025). Recalls, Market Withdrawals, & Safety Alerts. https://www.fda.gov/safety/recalls-market-withdrawals-safety-alerts