A Certificate of Analysis (COA) is a critical document in the supplement industry, ensuring that products meet the highest quality standards and comply with regulatory requirements. This essential document is an identification document that provides detailed information about a product’s specifications, chemical composition, and test results.
For supplement businesses, COAs are indispensable tools for verifying product quality, assuring customers of safety, and meeting industry standards. By presenting laboratory analyses and tests performed on raw materials and finished products, COAs help brands maintain customer trust, achieve regulatory compliance, and uphold quality assurance throughout their supply chain.
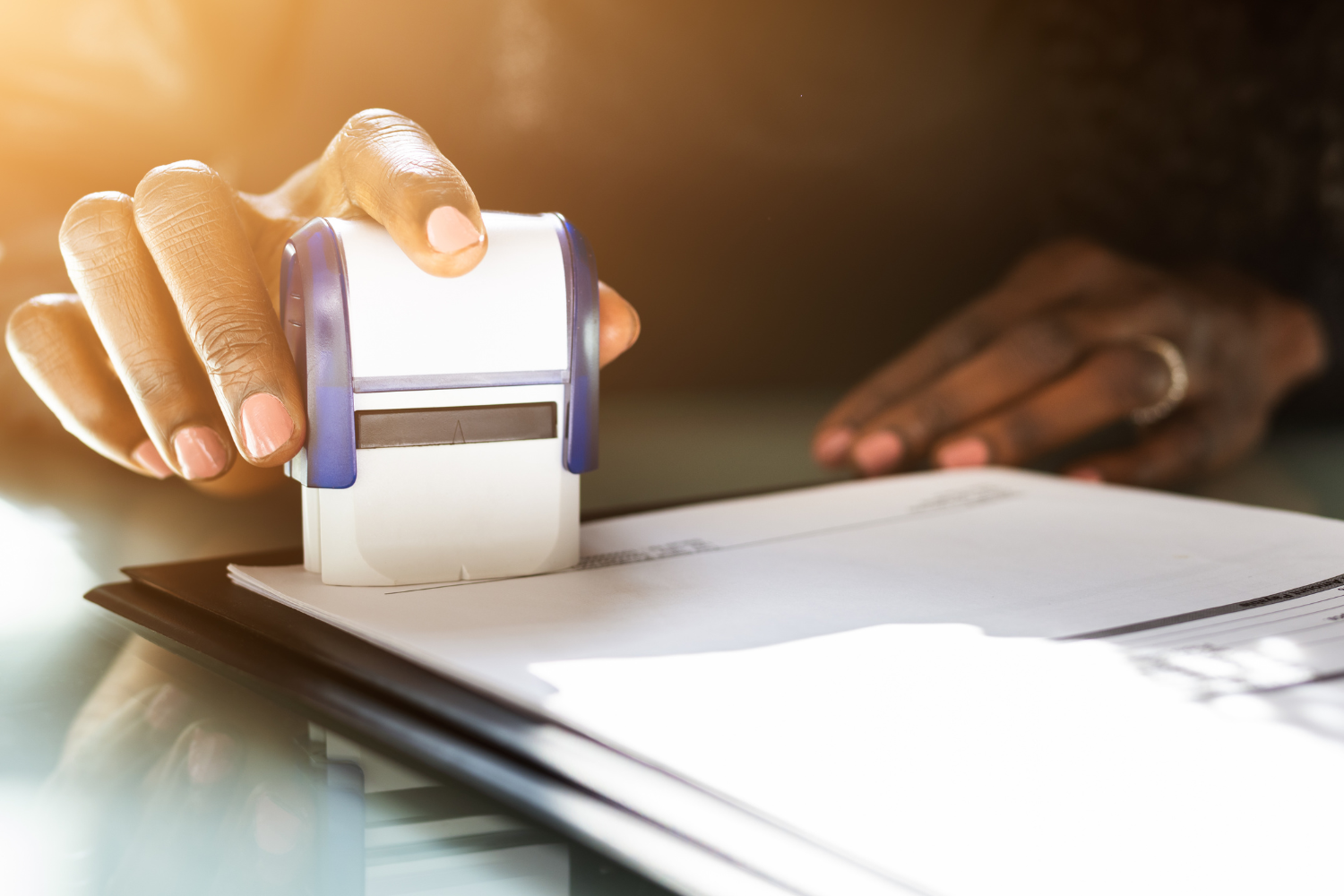
The Basics of a Certificate of Analysis (COA)
A Certificate of Analysis (COA) is a formal document that certifies a product’s quality and composition. Typically issued by third-party laboratories, it includes detailed analysis data to confirm that the product complies with specified standards. COAs are essential for ensuring that the product’s components meet industry quality control and safety standards.
This document is vital in confirming that a product meets its required specifications. Through laboratory analyses and detailed information about tests conducted, COAs verify that a product’s quality, physical properties, and chemical composition align with regulatory and customer requirements.
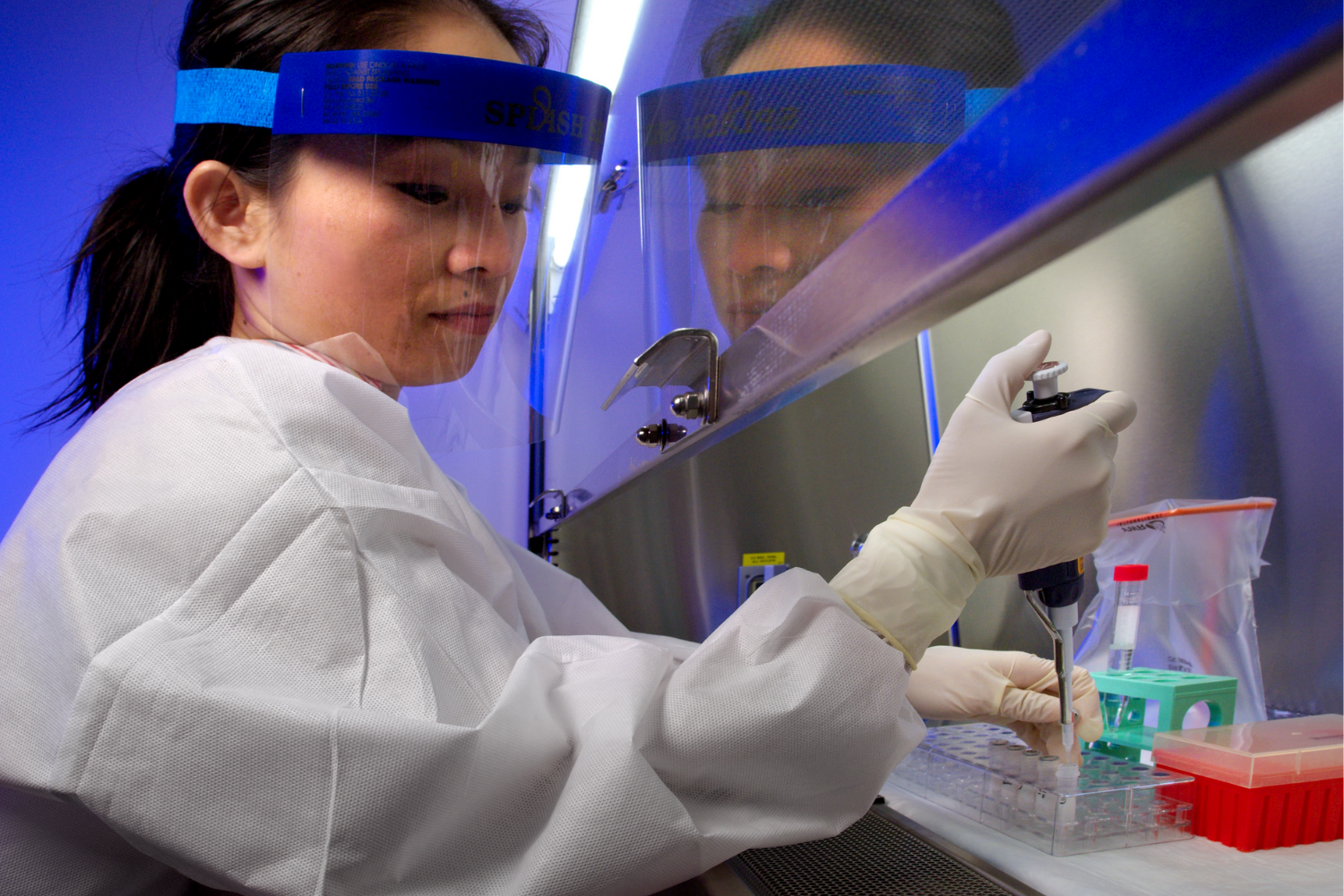
Why Do Supplements Need a COA?
In the supplement industry, COAs are crucial for proving a product’s purity, potency, and safety. Customers expect high-quality assurance, and a COA provides the evidence to meet those expectations. Analytical methods and laboratory tests validate that all the tests have been performed to ensure product compliance with quality requirements.
While COAs are not universally mandated, they are a highly recommended tool for ensuring product safety and regulatory compliance. This document helps brands build customer trust, assuring them that the supplement’s quality and safety align with regulatory and consumer expectations.
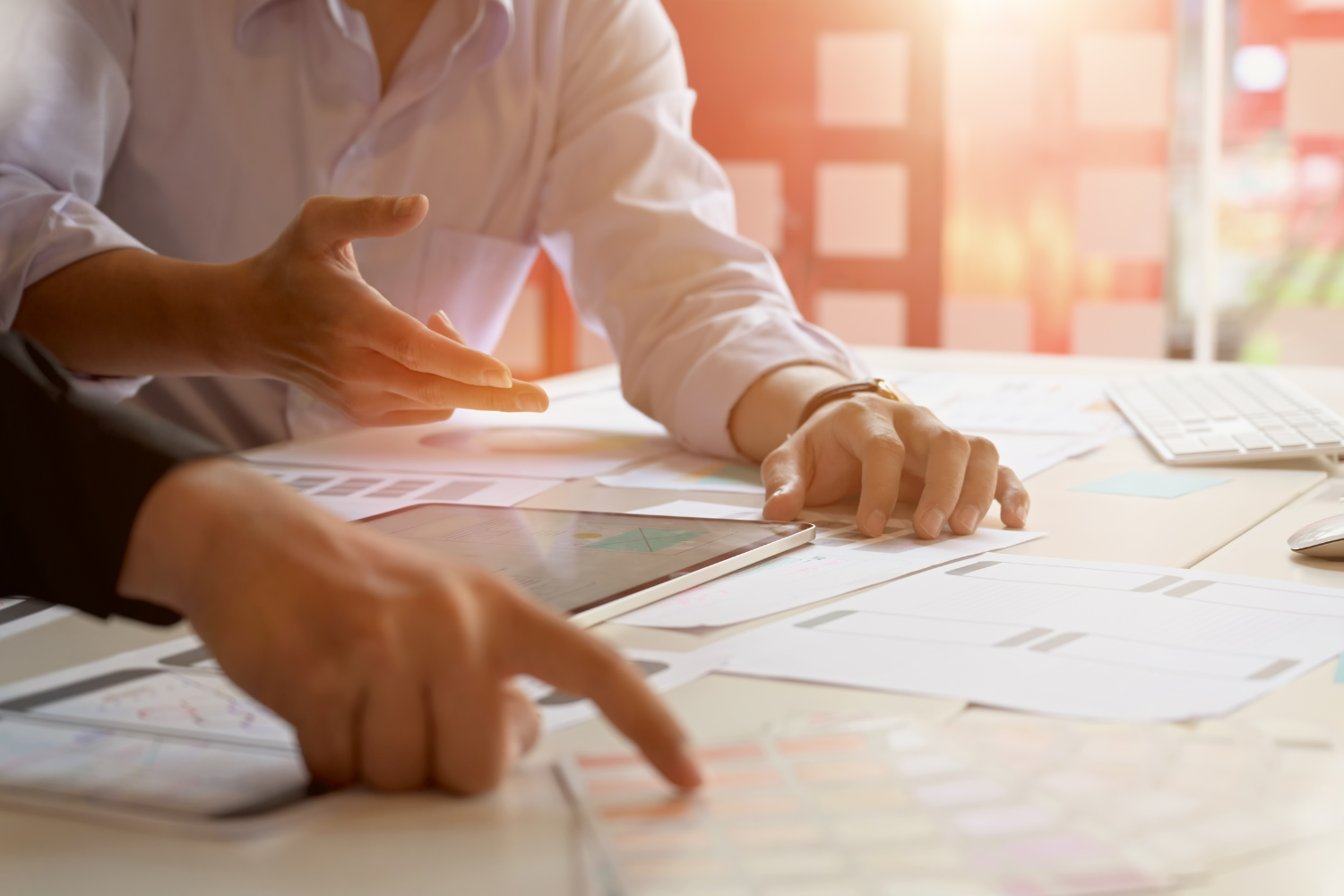
What Information Is Included in a COA?
A COA provides detailed information to confirm a product’s specifications. It serves as a comprehensive identification document for quality control checks. Critical components of a typical COA include:
- Ingredient list and concentrations
- Purity levels
- Test results for contaminants (e.g., heavy metals, pesticides)
- Microbiological analysis (e.g., mold, bacteria)
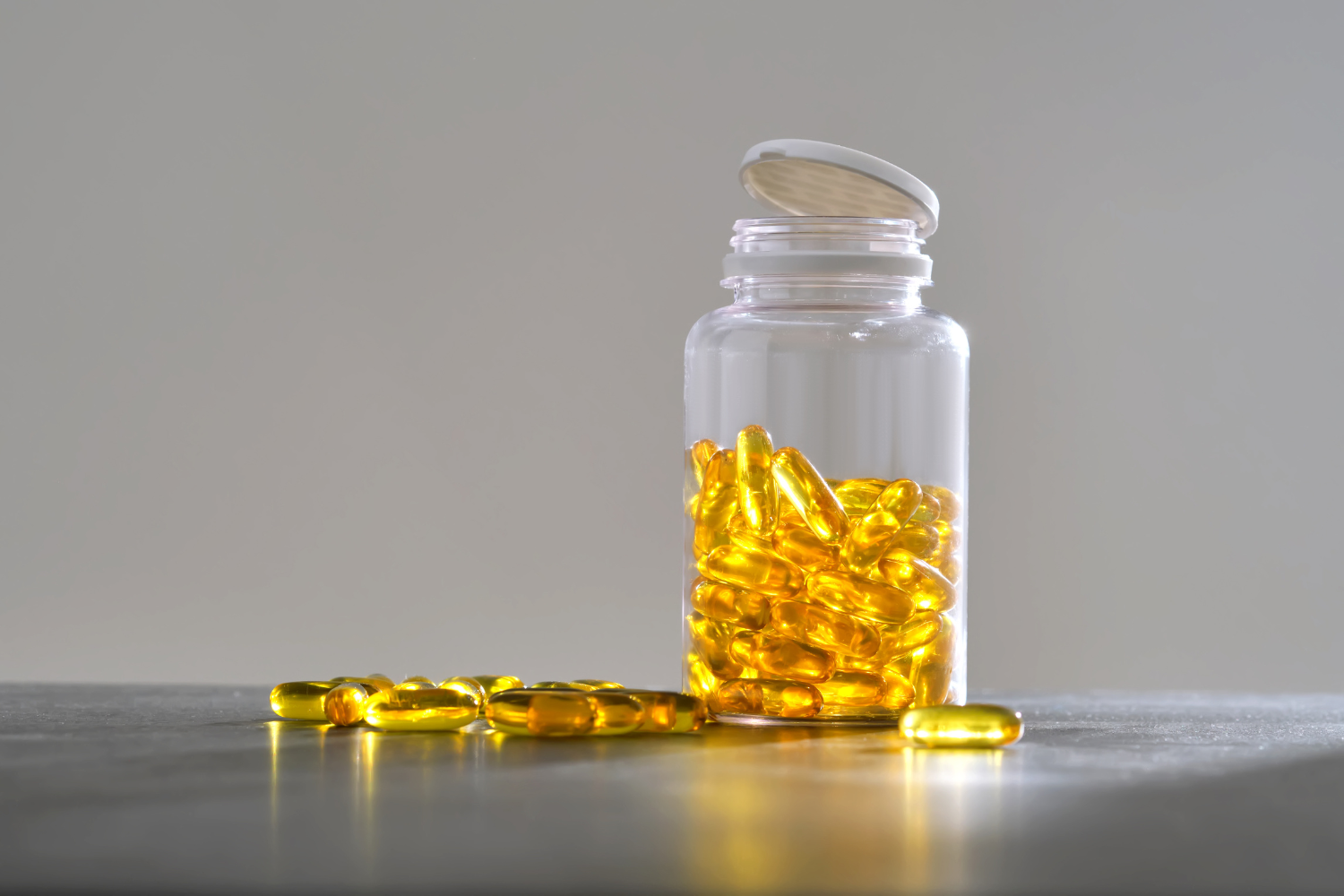
How to Read and Interpret a COA?
Interpreting a COA involves evaluating key details to ensure the product meets quality standards. Each section of the COA provides crucial information about the product’s compliance and specifications.
Step 1 – Check the Batch Number and Date
Verifying the batch number and manufacturing date is critical to ensure the COA matches the evaluated product. The batch number links the document to the product tested, while the test date confirms the results are recent. These details ensure that the product complies with regulatory standards and customer expectations.
Step 2 – Review the Ingredients and Potency
The ingredient list and potency data should be compared to the product’s label to verify the accuracy of the information provided. Ensuring the correct dosages and concentrations are listed helps maintain consistency and quality across batches. This step provides assurance that the product meets specified standards for consumer safety.
Step 3 – Analyze the Purity and Contaminant Results
COAs include chemical analysis results for contaminants like heavy metals, pesticides, and microbial agents. Confirming that levels of heavy metals such as lead or mercury are within acceptable limits helps reduce risks associated with contamination. Microbiological analyses should indicate no harmful bacteria, mold, or other microbial threats to ensure consumer safety.
These test results are vital for assessing product safety. Ensuring the product complies with regulatory standards and quality requirements helps minimize potential health risks.
Step 4 – Look for Third-Party Verification
Third-party testing ensures an unbiased evaluation of the product’s quality and compliance. Trusted certification bodies and testing facilities validate a product’s specifications using rigorous analytical methods.
Look for seals from reputable organizations, such as NSF International or Informed Choice, that verify that the COA data aligns with regulatory standards. Independent verification builds trust and ensures accuracy, which are fundamental elements of quality assurance.
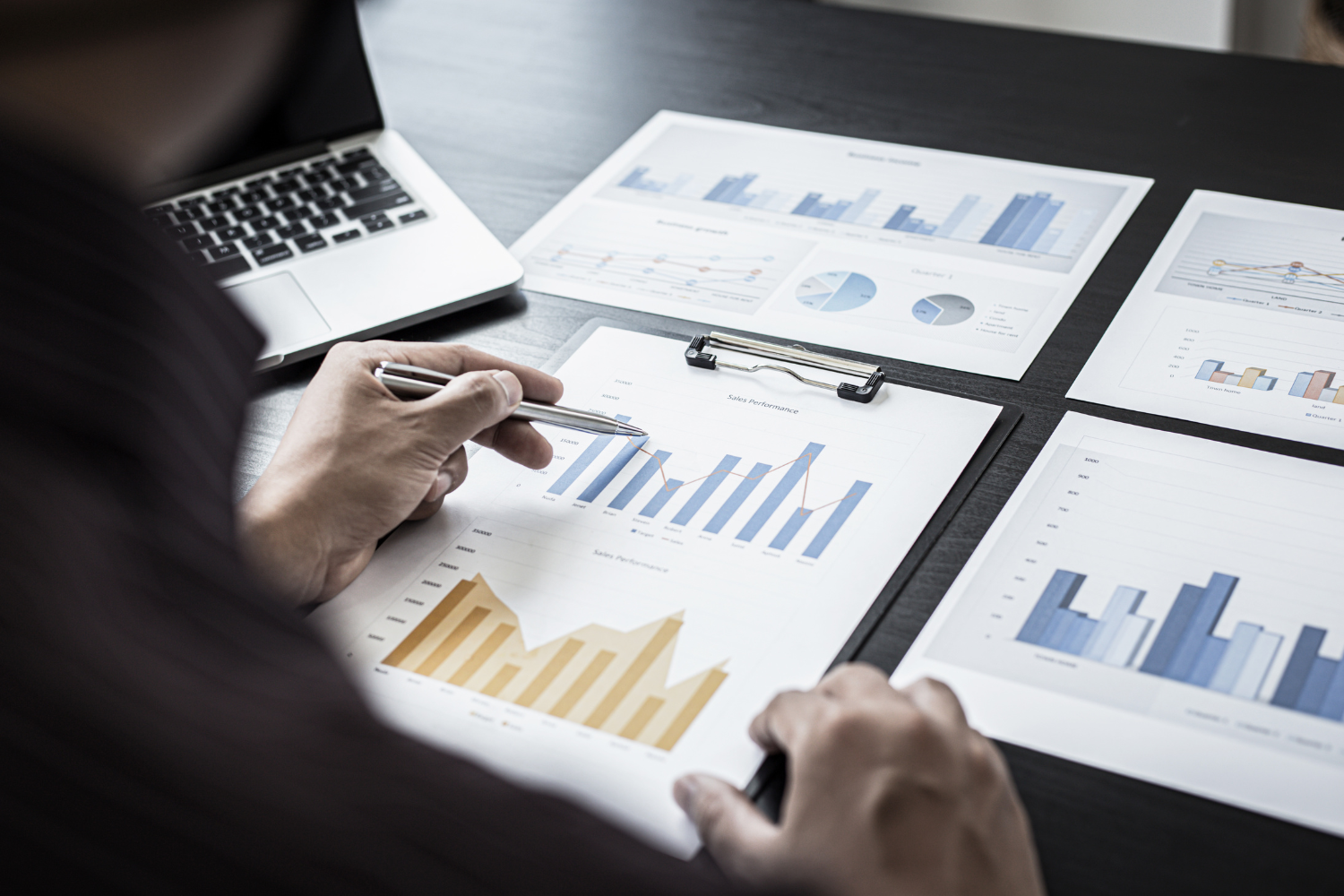
Why a COA Is Important for Your Supplement Brand
A Certificate of Analysis (COA) is essential for establishing trust, meeting regulatory requirements, and safeguarding your brand’s reputation. It ensures that your supplements meet quality assurance and regulatory compliance standards while protecting your business from potential risks.
Build Customer Trust with Verified Quality
Having a COA demonstrates your commitment to transparency, giving customers confidence in the safety and quality of your products. Detailed test results and analysis data from a trusted source demonstrate that your supplements are evaluated against strict quality standards. This builds loyalty and enhances your reputation in a competitive market with high customer expectations for safety and efficacy.
Compliance with Regulatory Standards
COAs play a crucial role in meeting the quality requirements set by regulatory bodies such as the FDA and NSF. They validate that your products meet quality and safety standards through laboratory analysis. Regulatory compliance ensures legal operations and aligns your brand with industry standards, fostering credibility with both consumers and certification bodies.
Protect Your Brand from Legal Risks
Legal risks, such as claims of mislabeling or contamination, can harm your brand’s reputation and lead to financial penalties. A COA helps safeguard your business by providing documented proof of the product’s compliance with quality control checks and regulatory standards. It is a protective measure to verify product safety and prevent potential issues.
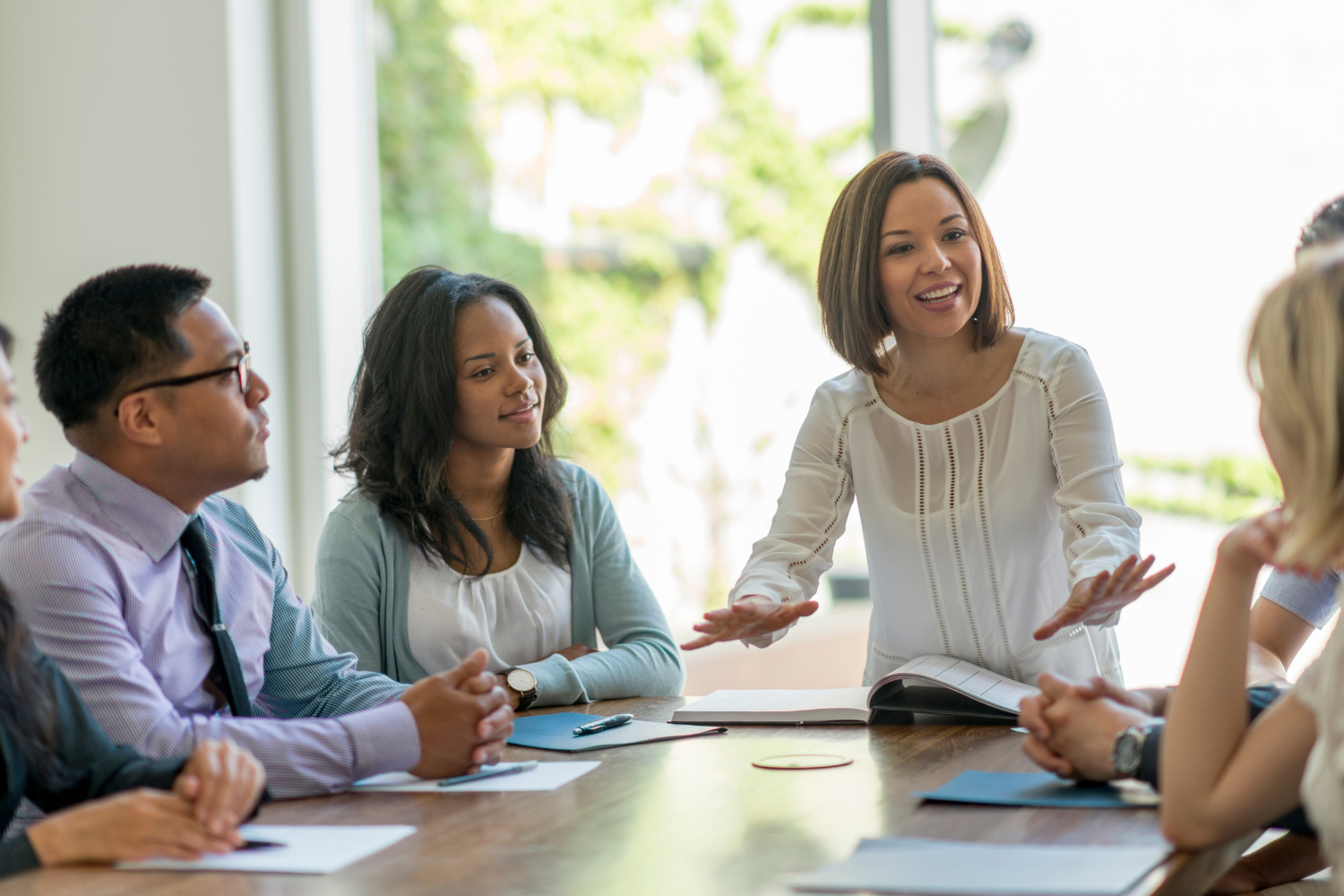
How to Obtain a Certificate of Analysis for Your Supplements
Obtaining a COA for your supplements is straightforward and involves collaboration with trusted manufacturers and third-party labs. Following these steps will ensure your products meet quality and safety standards.
Step 1 – Work with Reputable Manufacturers
Partnering with a reliable manufacturer is essential for obtaining COAs. GMP-certified manufacturers typically follow strict quality assurance processes and provide COA documents for their products. These manufacturers conduct thorough laboratory analyses to ensure raw materials and finished products comply with regulatory standards.
Working with a manufacturer who prioritizes quality control reduces manual tasks and ensures accurate documentation. This partnership forms the foundation for maintaining quality assurance throughout your supply chain.
Step 2 – Request Third-Party Testing
If your manufacturer does not provide COAs, you can arrange for independent testing by reputable third-party labs. These labs offer unbiased evaluations to verify your product’s quality and compliance. Trusted third-party testing facilities include:
- NSF International
- Eurofins Scientific
- Informed-Choice
- ConsumerLab
Step 3 – Review and Verify the COA Before Launching Your Product
Before finalizing product development, carefully review the COA to ensure the product meets quality standards and customer requirements. Focus on the following:
- Confirm the batch number matches the product.
- Verify ingredient concentrations align with product labels.
- Check for acceptable levels of contaminants such as heavy metals and pesticides.
- Ensure test results meet regulatory compliance and customer expectations.
Thorough COA management ensures your product’s quality and compliance, helping you confidently launch supplements in the market.
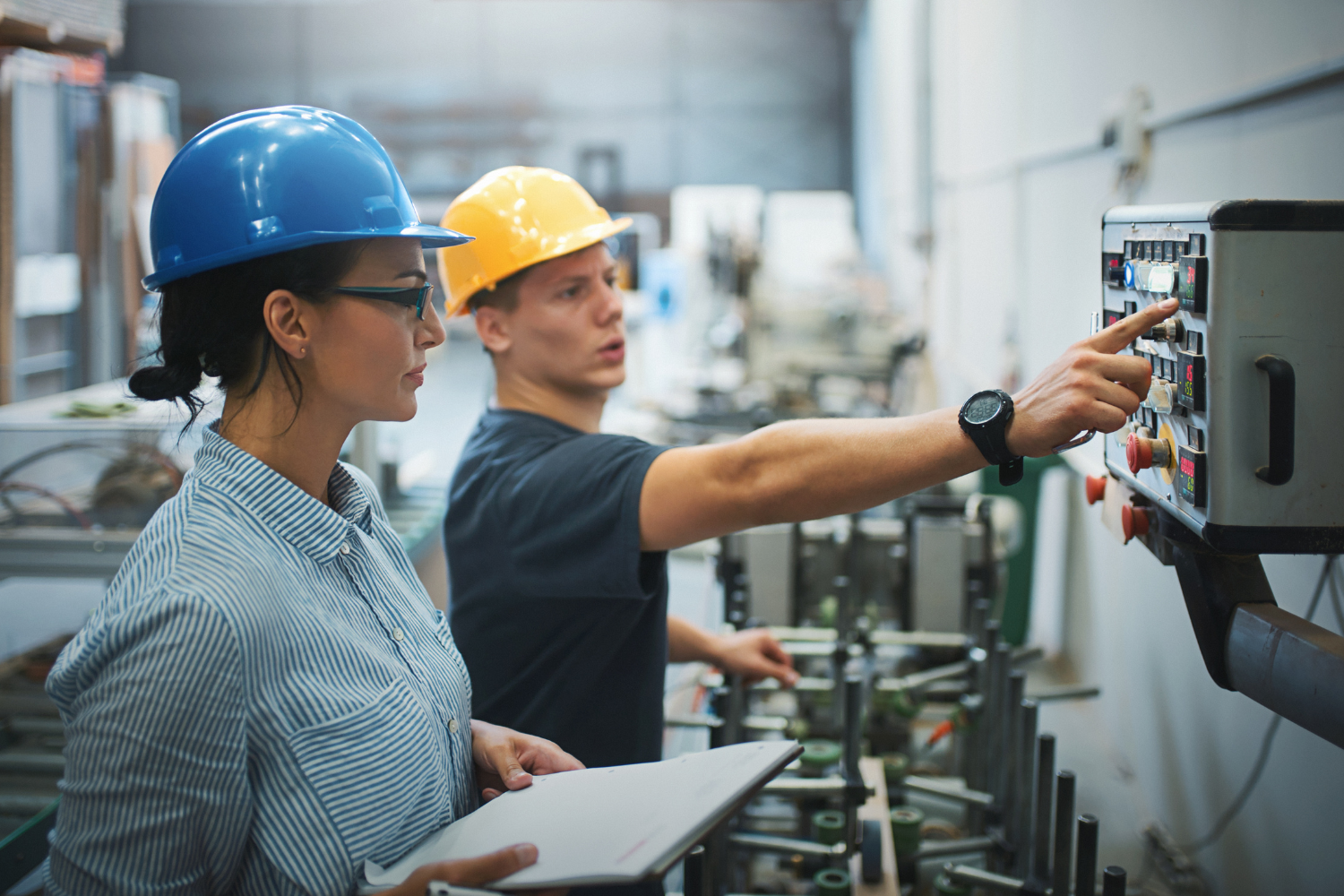
Common Questions About COAs
COAs are a critical element of quality assurance for supplement businesses, but there are often questions about their necessity and best practices. Understanding these details helps companies to stay compliant and ensure product quality.
Is a COA Required by Law for Supplements?
In regions like the US, COAs are not legally required for supplements but are highly recommended. The FDA regulates dietary supplements under the Dietary Supplement Health and Education Act (DSHEA), which mandates that products meet quality standards but does not specifically require COAs. Similar regulations apply in the EU. While COAs might not always be mandatory, they are vital for ensuring regulatory compliance, product quality, and consumer safety.
Can I Trust a Manufacturer Who Doesn’t Provide a COA?
A manufacturer that does not provide COAs may not follow best practices for quality assurance. This can be a red flag indicating a lack of transparency or quality control measures. If a manufacturer does not routinely offer COAs, request third-party testing or consider working with a GMP-certified manufacturer that prioritizes regulatory compliance and detailed quality analysis.
How Often Should I Request a COA for My Products?
Requesting a COA for each batch is a best practice for ensuring consistent quality, especially when raw materials or manufacturing conditions vary. Variations in raw materials or manufacturing processes can impact a product’s compliance with safety and quality standards. Regularly obtaining and reviewing COA helps maintain customer trust and ensures adherence to regulatory requirements across all manufacturing sectors.
The Importance of COAs for Your Supplement Business
A Certificate of Analysis is essential for maintaining your supplements’ quality, safety, and regulatory compliance. It protects your brand, ensures consumer safety, and builds customer trust through verified quality. Making COAs a non-negotiable part of your supplement business strategy is key to upholding industry standards, safeguarding your reputation, and delivering products that meet customer expectations and regulatory demands.
Frequently Asked Questions
How Can I Verify the Authenticity of a COA?
Verify a COA’s authenticity by checking for third-party verification, confirming the laboratory’s credentials, and cross-referencing the batch number with product details.
What Happens If a COA Reveals Contaminants?
If a COA reveals contaminants, address the issue immediately by halting production, consulting with the testing facility, and revising your quality control processes.
Can I Use a COA as a Marketing Tool?
COAs can be showcased to consumers to highlight transparency and quality assurance, building trust and reinforcing your brand’s commitment to safety and compliance.
Do COAs Apply to Other Industries Besides Supplements?
Yes, COAs are used across various industries, including pharmaceuticals, chemical manufacturing, and food products, to verify compliance and product quality.
What Should I Do If a Manufacturer Refuses to Provide a COA?
If a manufacturer refuses to provide a COA, consider this a red flag. Opt for third-party testing or switch to a reputable GMP-certified manufacturer.
References
- Code of Federal Regulations. (2024). eCFR :: 21 CFR Part 111 Subpart E—Requirement to Establish a Production and Process Control System. https://www.ecfr.gov/current/title-21/chapter-I/subchapter-B/part-111/subpart-E
- U.S. Food and Drug Administration. (2024). CFR – Code of Federal Regulations Title 21. https://www.accessdata.fda.gov/scripts/cdrh/cfdocs/cfcfr/cfrsearch.cfm
- U.S. Food and Drug Administration. (2024). Guidance Documents & Regulatory Information by Topic (Food and Dietary Supplements). https://www.fda.gov/food/guidance-regulation-food-and-dietary-supplements/guidance-documents-regulatory-information-topic-food-and-dietary-supplements
- U.S. Food and Drug Administration. (2024). Information for Industry on Dietary Supplements. https://www.fda.gov/food/dietary-supplements/information-industry-dietary-supplements
- U.S. Food and Drug Administration. (2018). Q7A Good Manufacturing Practice Guidance for Active Pharmaceutical Ingredients. https://www.fda.gov/regulatory-information/search-fda-guidance-documents/q7a-good-manufacturing-practice-guidance-active-pharmaceutical-ingredients
- U.S. Food and Drug Administration. (2018). Small Entity Compliance Guide: Current Good Manufacturing Practice in Manufacturing, Packaging, Labeling, or Holding Operations for Dietary Supplements. https://www.fda.gov/regulatory-information/search-fda-guidance-documents/small-entity-compliance-guide-current-good-manufacturing-practice-manufacturing-packaging-labeling